Al Haase, President and CEO of AGC Composites & Aerostructures Group shares, “Two of our companies, Unitech Composites and Integrated Composites, each utilize DMS 5 Axis CNC Routers in their operations, and we’re extremely proud that our high-quality products and systems support the commercial and general aviation market, as well as a wide range of U.S. military platforms.” When a Soldier on the battlefield calls for aerial support, it’s likely that a Kiowa Warrior or Chinook helicopter will arrive on the scene. The Bell OH-58 Kiowa Warrior is an armed scout attack helicopter, and the Boeing CH-47 Chinook is a twin-engine, tandem rotor heavy-lift helicopter, used for cargo and troop transport.
Composite Universal Weapons Pylon
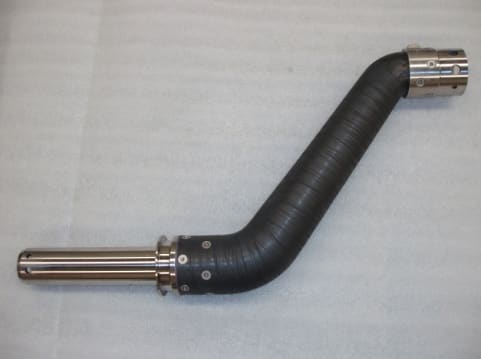
Located in Marina, California, Integrated Composites manufactures the lightweight Composite Universal Weapons Pylon (CUWP), which is mounted on the sides of the OH-58D Kiowa Warrior helicopter. “The CUWP was an original design by our team in order to help reduce weight on the aircraft,” said Preston Sandusky, Chief Operating Officer for Integrated Composites. “We have since transitioned into high volume manufacturing as demand has grown within the U.S. Army,” he added. The CUWP provides an important attack capability for the pilots, and the carbon composite material reduces the weight load on the helicopter. “Initially, profiling the ends of the composite pylon tube was done by hand, which was very time consuming, and this created a dilemma as we faced increasing demand for the product,” said Sandusky. The solution was the DMS 5 Axis CNC Router, which was the cost-effective solution for trimming the carbon tube profile for bonding of the inboard and outboard titanium fittings of the CUWP,” said Sandusky.
Maintenance Walkway Panel
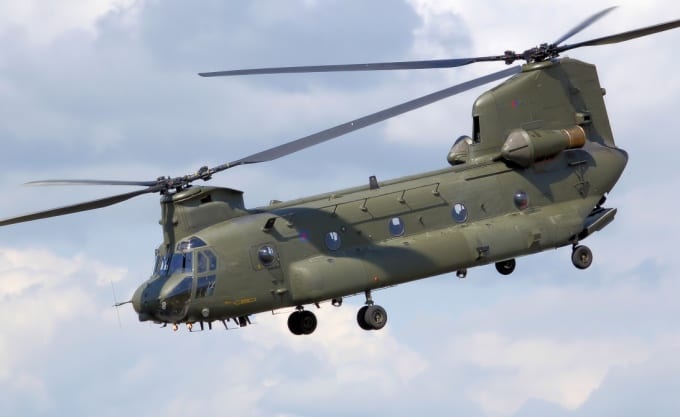
At Unitech Composites in Hayden, Idaho, they support Army Aviation by manufacturing products such as the Maintenance Walkway Panel for the CH-47 Chinook helicopter. Located at the rear of the helicopter, directly below the rear rotor assembly, the panel can be opened and extend down to serve as a maintenance platform for the aircraft maintenance personnel to stand on to do their work. “We manufacture over 150 panels a year for CH-47 aircraft” said Tim Shuburg, Director of Operations for Unitech Composites. “In the past we were cutting these parts manually, which was very labor intensive and caused excessive scrap. This prior approach limited our ability to produce large volumes of parts,” he added.
Labor Savings
As the complexity and precision of composite parts increases, advanced manufacturing capabilities are necessary to remain competitive within the aerospace industry. “When we implemented the DMS 5 Axis CNC Router it provided substantial savings in labor, as well as greater accuracy of the trimmed part – which in turn reduced scrap. Also, we don’t use our machine to rotate into position; we use all 5 Axes at the same time during the cutting. We can keep our cutter true to the design of the engineers, so that manual processes are minimized. Our capacity has more than doubled since adding the 5 Axis machine,” said Shuburg.
Inspection Process
Another problem with the manual approach in the past was evident in the time consuming inspection process. Unitech Composites also utilizes their DMS 5-Axis to inspect parts. “The only true way to check the measurement of a flexible fiberglass part trim, would be to leave it on the fixture in the position it was trimmed. With a Probe attachment and Delcam software, we’re able to mimic the machine movements and create the surface placement in space, without allowing it to move into a new position” said Shuburg. “In the past we had to try and recreate the holding scenario in QA, now we can check it in its natural state without moving the part, it can probe each point and compare to the model. The accuracy is within 0.002”, and the measurement data is formatted into a document that we provide to our customers as a first article inspection report.” added Shuburg. The requirement for state-of-the-art technology is apparent in the aerospace industry, and the importance is most evident in supporting our nation’s military during a time of war. “We are fully committed to the highest standards of quality and continuous improvement in serving our customers, and tangible evidence of this is how we utilize the DMS solution in our manufacturing,” said Al Haase. Click Here to see the JEC Composites MagazineÂ