From 3 to 5-Axis in 30 Seconds on The Hybrid 2 Cubed
At DMS we are committed to advancing metal-additive manufacturing. So we continue to push the envelope with our Hybrid additive/subtractive process, this time by adding 5-axis capabilities to our turn-key Hybrid 2 Cubed metal-additive machine.
Our Hybrid 2 Cubed is a popular choice because of its small footprint, economical price and 2’x2’x2’ build volume. This machine is the perfect entry point into large format, metal additive manufacturing — as long as 3-axis capabilities are sufficient. For people seeking the benefits of the original Hybrid 2 Cubed but occasionally requiring a 5-axis solution, this innovation was designed with you in mind. A 5-axis table, mounted on linear rails, allows the user to choose the Hybrid 2 Cubed’s original 2’x2’x2’ build volume or the 15”x15” cylindrical 5-axis build volume. You can engage or withdraw the 5-axis table in under 30 seconds. With the 5-axis table engaged the 30º-45º overhang limits are removed, greatly expanding the possible geometries.
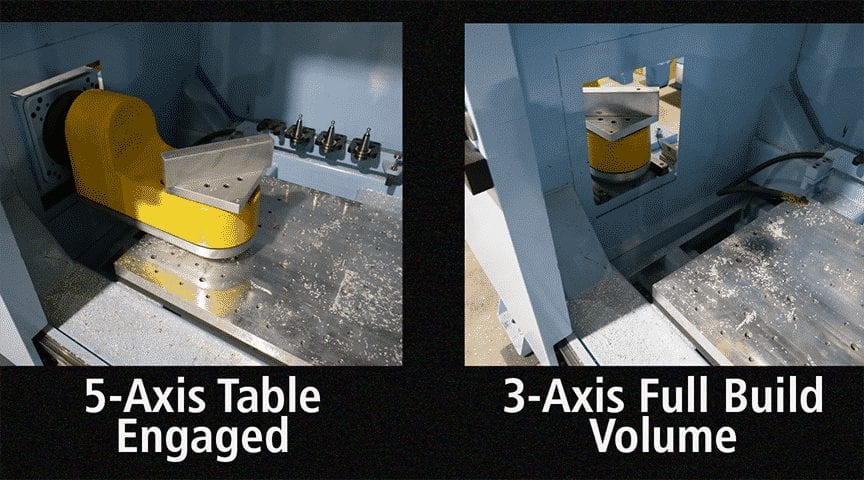
In one of our case studies, this process greatly improved the manufacturing of propellers and impellers where the low-volume production run makes casting cost-prohibitive. When you compare our Hybrid process to traditional subtractive machining from billet, far less material is used, and machining between additive intervals makes more complex designs possible. Compared with casting, the time and cost from design to testing is significantly reduced, as no special tooling is required to be built and tested.
In our 5-axis Hybrid 2 Cubed, the total build time of this propeller was 15 hours and is ready to be finish-machined.